Actual Costing vs. Standard Costing – What You Need to Know about Costing Methods for Manufacturing
A costing method is the framework within an ERP system for monitoring inventory, profitability, and costs. It is crucial for organizations to keep track of these levels to maximize profits and minimize wasted cash flow. Read more on these topics below.
Selecting the correct costing method is an integral part of efficient business practices, especially in the manufacturing industry. Organizations must consider how they want to value inventory, and how they should book the cost of goods sold to best monitor the performance of the business.
The most followed for Best practices are two costing methodologies are:
- Actual Costing: records actual costs and actual inventory values using lot control disciplines, without incorporating budgeted or standard amounts
- Standard Costing: measures costs incurred against standard values, providing variance analysis for monitoring performance and efficiency
Below is an explanation of the nuances involved when choosing standard or actual costing for a manufacturing business.
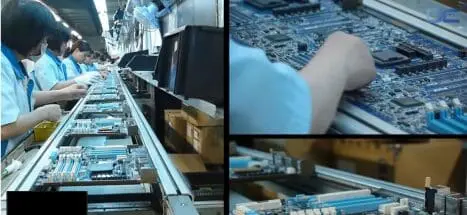
Standard Costing
At ERTechnologies we usually recommend businesses in the manufacturing industry use standard costing. A standard cost system has the highest level of cost control, cost integrity, and financial stability. Standard costing measures day-to-day values of inventory and cost of goods sold against (“standard”) levels. This gives businesses a basis for comparison, and puts the company on track towards a migration to lean costing methodologies during lean manufacturing implementations. Standard Costing also enables variance analysis to measure the company’s costs and provide insight into the success of the business. Common variance analysis includes: purchase price, engineering, planned, actual, and other variances.
The main decision that must be made when an organization utilizes standard costing is determining how often the standards should be set. Accurate reporting depends on continuous analysis, so businesses must choose how often they analyze their costs. It’s common to track and post current costs daily and compare against frozen costs to determine if new standards should be frozen sooner than the company’s policies and procedures dictate.
Why Businesses Consider Switching Costing Methods
A costing method is usually embedded in a company’s busines practices, and operations are build around it. When implementing new software, it is important to evaluate the effectiveness of the current costing method. Both costing methods have pros and cons. The main difference between the two is how businesses want to value inventory and classify their cost of goods sold.
Though most manufacturing businesses already use standard costing, many consider switching to actual for increased flexibility and more frequent reporting without variance analysis. Businesses that switch to actual costing should be prepared to:
- Invest in shop floor data collection automation
- Make a paradigm shift to managing inventory at a lot or serial level
Switching to actual costing can be quite difficult for manufacturing businesses. Because it requires such precise measurement, employees on the production floor must meticulously track all material costs and inventory at the highest level, which can be a time-consuming process.
Actual Costing
It’s best to use actual costing in very particular cases. Because actual costing must track the exact inventory values and cost of goods sold for each order, this method is most effective when a business produces a highly-configurable product, or has varying or unpredictable customer needs. Actual costing is virtually the only option for configurable product manufacturing where customers have many features and options to choose from when placing orders. These orders can’t be anticipated and thus will not match a standard budget. Actual costing offers flexibility and exact costing, but has no standard of comparison. This is best when a company cannot anticipate the many combinations or permutations of potential orders.
Summary
As with most business decisions, the execution is the determining factor of success for these costing methods. Both methods require discipline, and knowledge from the organization regarding:
- What the business needs from its costing method
- How to report costs in a way that complements existing business processes
ERTechnologies can assist to identify these needs and facilitate this execution for ultimate results and ERP optimization, and to help identify the method that will provide the highest level of cost control, cost integrity, and financial stability.
About ERTechnologies as your Cloud Partner?
ERTechnologies is the leading Oracle partner delivering The Oracle Manufacturing Cloud for manufacturers. ERT has pioneered cloud solutions for the shop floor, connecting suppliers, machines, people, systems, and customers with capabilities that are easy to configure, deliver continuous innovation, and reduce IT costs. With insight that starts on the production floor, we help manufacturers see, understand and uncover the value hidden in their Oracle technology investments by capturing unexpected opportunities to fuel growth and profitability in every aspect of their business ecosystems, enabling them to lead in ever-changing markets using Oracle technologies.
Learn more at www.ER-Technologies.com | (949) 387-0250