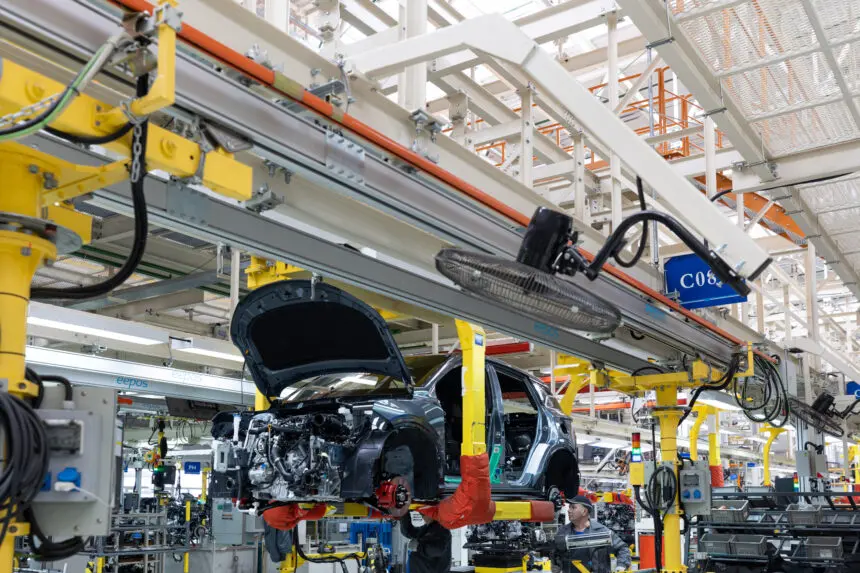
Smart Manufacturing: Driving Digital Transformation
Smart Manufacturing: Driving Digital Transformation
Introduction
The manufacturing industry is undergoing a seismic shift driven by digital transformation. The concept of smart manufacturing is central to this evolution, leveraging cutting-edge technologies to enable manufacturers to operate more efficiently, flexibly, and competitively. Smart manufacturing represents a convergence of digital technologies such as the Industrial Internet of Things (IIoT), Artificial Intelligence (AI), big data, analytics, and automation, all working together to create a more intelligent, connected, and optimized manufacturing ecosystem known as smart factory 4.0.
Digital Transformation and Smart Manufacturing
Digital transformation is the integration of digital technologies into every aspect of a business, fundamentally changing how it operates and delivers value to customers. In the context of manufacturing, digital transformation is driven by adopting smart manufacturing solutions. Smart manufacturing enables manufacturers to harness the power of data, analytics, and automation to improve operational efficiency, enhance product quality, and reduce costs. This evolution is crucial for smart factories aiming to stay competitive.
Smart manufacturing is not just about automating existing processes; it’s about rethinking the entire manufacturing value chain to create new ways of producing goods and delivering value. This transformation allows manufacturers, including small & medium manufacturers, to become more agile, responsive, and resilient in an increasingly complex and competitive global market.
What is Smart Manufacturing?
Smart manufacturing is a comprehensive approach that integrates advanced technologies to optimize production processes, improve product quality, and increase overall operational efficiency. At its core, smart manufacturing 4.0 creates a connected smart manufacturing environment where machines, systems, and humans work together seamlessly.
Key Components of Smart Manufacturing:
- Industrial Internet of Things (IIoT): IIoT connects machines, sensors, and devices to the Internet, enabling real-time data collection and communication across the manufacturing ecosystem. This connectivity allows for more precise monitoring, control, and optimization of manufacturing processes, forming the backbone of smart factory solutions.
- Artificial Intelligence (AI): AI powers predictive analytics, machine learning, and decision-making algorithms that enhance the efficiency and effectiveness of manufacturing operations. AI-driven systems can predict equipment failures, optimize production schedules, and improve quality control within smart manufacturing.
- Big Data and Analytics: The massive amounts of data generated by connected machines and systems are analyzed using advanced analytics tools to gain insights into production processes, identify inefficiencies, and drive continuous improvement—key aspects of a smart factory.
- Automation: Automation involves using robotics, computer-controlled machinery, and automated workflows to perform repetitive tasks, reduce human error, and increase production speed. Automation is a key enabler of smart manufacturing, allowing for more consistent and reliable production processes.
Optimized Workforce: In a smart manufacturing environment, the human workforce is empowered with digital tools and technologies that enhance their productivity and decision-making capabilities. Training and upskilling employees to work alongside advanced technologies are crucial for the successful implementation of smart manufacturing.
https://youtu.be/WAKlXBXtoWI?feature=shared
Key Benefits of Smart Manufacturing
Increased Efficiency
One of the most significant benefits of smart manufacturing is the increased efficiency in production processes. By automating repetitive tasks, smart manufacturing reduces the time and effort required to produce goods. Real-time monitoring and data analytics enable manufacturers to identify and address inefficiencies, leading to more streamlined and cost-effective operations, which is essential for small and medium manufacturers. This is especially critical when implementing an ERP system for small manufacturers as it helps align production goals with digital capabilities, driving digital transformation across the entire operation.
Automated Processes
Automation is a cornerstone of smart manufacturing. Automated processes reduce the reliance on manual labor, minimize errors, and speed up production. This leads to higher throughput and enables manufacturers to meet increasing demand without compromising quality, a vital aspect for smart factories. For industries such as medical devices, implementing NetSuite for medical device manufacturers can streamline these automated processes, ensuring compliance and enhancing productivity.
Real-Time Monitoring and Analytics
Smart manufacturing systems provide real-time visibility into every aspect of the production process. Sensors and connected devices continuously collect data, which is then analyzed to monitor performance, detect anomalies, and optimize operations. Real-time analytics enable manufacturers to make informed decisions quickly, improving overall operating efficiency within smart factories. For small businesses, an ERP system for small manufacturers integrated with real-time monitoring capabilities can be transformative, enhancing decision-making and resource allocation. This is particularly true for industries like automotive and aerospace, where an ERP system for the automotive industry and ERP software for aerospace suppliers must handle complex operations with precision.
Overall Operating Efficiency and Predictive Maintenance
Smart manufacturing enables predictive maintenance by using data from connected machines to predict when equipment will likely fail. By addressing maintenance issues before they cause downtime, manufacturers can reduce unplanned outages and extend the lifespan of their equipment. This proactive approach to maintenance improves overall operating efficiency and reduces costs, contributing to the resilience of smart manufacturing. For small and medium manufacturers, implementing ERP systems for small businesses that support predictive maintenance can be a game-changer, driving digital transformation while ensuring operational continuity. Whether in the automotive, aerospace, or medical device sectors, the right ERP system, such as NetSuite for medical device manufacturers, can significantly enhance operational efficiency and resilience.
Enhanced Quality Control and Cost Reduction
Smart manufacturing significantly enhances quality control by providing real-time insights into production processes. Automated quality checks and AI-driven analytics identify defects and deviations early in the production cycle, allowing manufacturers to address issues before they impact the final product. This leads to higher product quality, reduced waste, and lower costs.
Cost Reduction
Smart manufacturing helps manufacturers lower operational costs by optimizing production processes, reducing waste, and improving resource utilization. Integrating automation and AI-driven systems further contributes to cost savings by reducing the need for manual labor and minimizing errors, making it a key strategy for small and medium manufacturers.
Smart Manufacturing: Connected Machines and Equipment
Smart manufacturing is characterized by the connectivity of machines, equipment, and systems across the production environment. This connectivity enables seamless communication and data exchange, allowing for more coordinated and efficient operations—a hallmark of smart factory 4.0.
Key Features of Smart Manufacturing:
- Connected Smart Manufacturing: Connected manufacturing involves integrating machines, sensors, and systems into a unified network that facilitates real-time data sharing and collaboration. This connectivity enables manufacturers to monitor and control production processes more effectively, improving efficiency and product quality within smart factories.
- Connected Machines and Equipment: In a smart manufacturing environment, machines and equipment are equipped with sensors and IoT devices that collect and transmit data in real-time. This data monitors machine performance, optimizes production schedules, and predicts maintenance needs, forming a critical component of smart manufacturing 4.0.
Smart Factory Solutions
Definition and Scope
A smart factory is a fully connected and digitized production facility that uses advanced technologies to optimize manufacturing processes, improve product quality, and increase operational efficiency. Smart Factories 4.0 leverages IIoT, AI, big data, and automation to create a more intelligent and responsive production environment.
Core Technologies
Smart factory solutions are built on a foundation of core technologies that enable seamless connectivity, data integration, and automation. These technologies include:
- Industrial IoT (IIoT): Enables real-time data collection and communication between machines, systems, and humans within smart factories.
- Artificial Intelligence (AI): Powers predictive analytics, machine learning, and decision-making algorithms.
- Big Data and Analytics: Provides insights into production processes and drives continuous improvement.
- Automation: Involves using robotics, automated workflows, and computer-controlled machinery.
- Digital Twins: Virtual replicas of physical assets that allow manufacturers to simulate and optimize production processes in real-time.
Adopting Smart Manufacturing
Adopting smart manufacturing is essential to staying competitive in the rapidly evolving manufacturing landscape. Start your journey towards digital transformation today by exploring our smart manufacturing solutions.
Contact us to learn how we can help you optimize your production processes, improve quality, and reduce costs in your smart factory.
Challenges and Considerations
While the benefits of smart manufacturing are substantial,manufacturers must addresse several challenges and considerations to ensure successful implementation.
Implementation Barriers
Implementing smart manufacturing requires significant investment in technology, infrastructure, and workforce training. Manufacturers may need help integrating new technologies with existing systems and resistance to change from employees, especially in small & medium manufacturers.
Data Security and Privacy
The increased connectivity of machines and systems in smart manufacturing environments raises data security and privacy concerns. Manufacturers must implement robust cybersecurity measures to protect sensitive information and prevent unauthorized access to critical systems, a priority in connected smart manufacturing.
Workforce Adaptation
The shift to smart manufacturing requires a workforce skilled in digital technologies and comfortable working alongside automated systems. Manufacturers must invest in training and upskilling employees to ensure they can effectively operate and maintain smart manufacturing systems.
Future Trends in Smart Manufacturing
Emerging Technologies
The continued development and adoption of emerging technologies will shape the future of smart manufacturing. These include advancements in AI, machine learning, blockchain, and 5G connectivity, which will further enhance the capabilities of smart factory 4.0 systems.
Sustainability and Smart Manufacturing
Sustainability is becoming an increasingly important focus for manufacturers. Smart manufacturing can contribute to sustainability efforts by optimizing resource utilization, reducing waste, and minimizing the environmental impact of production processes. Manufacturers will likely adopt more sustainable practices, such as using renewable energy sources and implementing circular economy principles, all within the framework of smart factories.
Conclusion
Smart manufacturing is transforming the industry by enabling digital transformation and driving significant efficiency, quality, and cost-effectiveness improvements. Manufacturers can create more connected, intelligent, and resilient production environments by leveraging advanced technologies such as IIoT, AI, big data, and automation within smart factories. While there are challenges to overcome, the benefits of smart manufacturing make it a critical component of the future of manufacturing, especially for small & medium manufacturers.
Frequently Asked Questions
What is Smart Manufacturing, and how does it differ from traditional manufacturing?
Smart manufacturing integrates advanced technologies like the Industrial Internet of Things (IIoT), Artificial Intelligence (AI), big data, and automation to optimize production processes, improve product quality, and increase operational efficiency. Unlike traditional manufacturing, which relies heavily on manual processes, smart manufacturing creates a connected and automated environment where machines, systems, and humans work together seamlessly, leading to a more agile and responsive manufacturing operation.
How does smart manufacturing contribute to digital transformation in the manufacturing industry?
Smart manufacturing is a key driver of digital transformation in the manufacturing industry. By adopting technologies like AI, IIoT, and automation, manufacturers can harness real-time data, improve operational efficiency, enhance product quality, and reduce costs. This transformation allows manufacturers to rethink their value chains, making them more competitive and resilient in the global market.
What are the key benefits of implementing smart manufacturing in a factory?
The key benefits of smart manufacturing include increased efficiency, enhanced quality control, cost reduction, real-time monitoring, and predictive maintenance. These benefits are achieved through automation, AI-driven analytics, and connected systems, which help streamline production processes, reduce human error, and optimize resource utilization.
What challenges should manufacturers expect when transitioning to smart manufacturing?
Transitioning to smart manufacturing can present challenges such as the need for significant investment in technology and infrastructure, workforce adaptation to new digital tools, data security concerns, and the complexity of integrating new technologies with existing systems. Addressing these challenges is crucial for the successful implementation of smart manufacturing.
How can smart manufacturing support sustainability efforts in the manufacturing industry?
Smart manufacturing supports sustainability by optimizing resource utilization, reducing waste, and minimizing the environmental impact of production processes. Manufacturers can implement sustainable practices, such as using renewable energy sources and adopting circular economy principles, to achieve more eco-friendly operations within smart factories.
Categories
- 1w
- 888starz bd
- anchorage escort service
- bbrbet colombia
- book of ra it
- casino
- casino en ligne fr
- casino onlina ca
- Food and Beverage Industry
- melhor cassinos online
- mostbet GR
- mostbet norway
- NetSuite for Manufacturing Business
- online casino au
- ricky casino australia
- Smart Manufacturing
- Tech Tips for Business Owners