End-to-end Supply Chain Visibility and Transparency
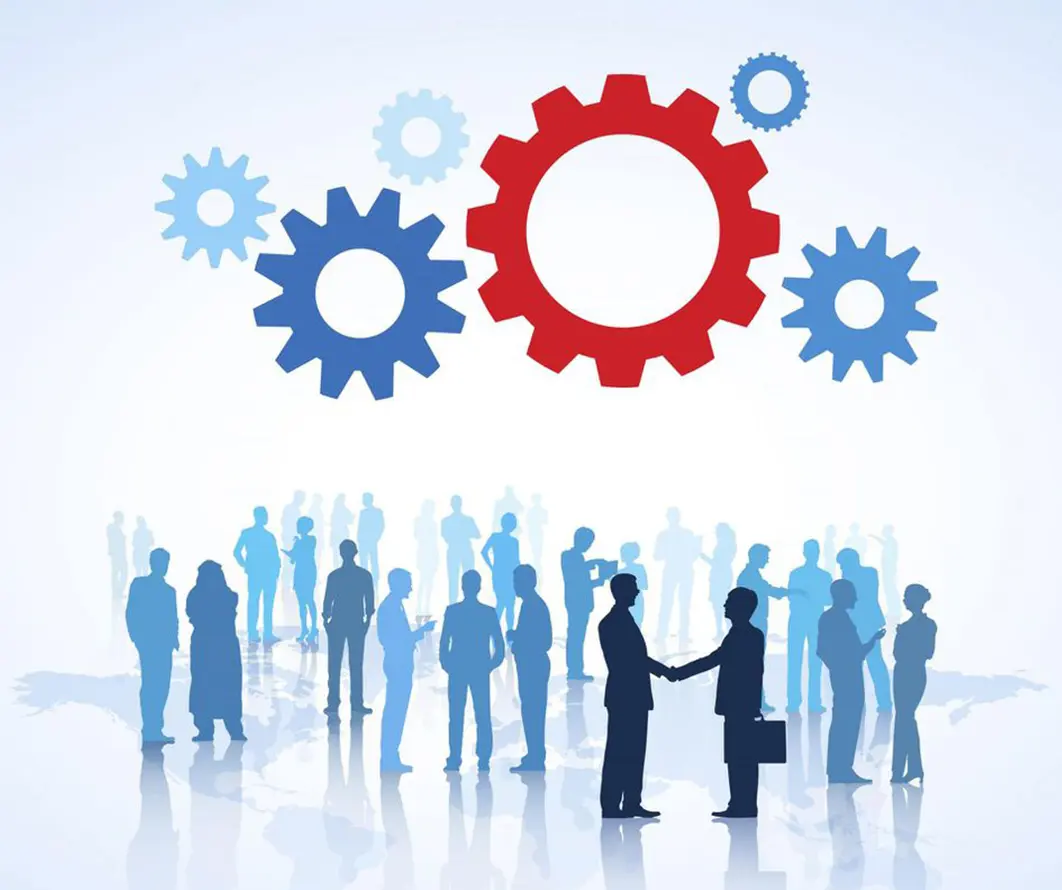
Most manufacturing companies use some type of traceability system, also known as Track and Trace, to comply with customer and market mandates as well as to have product genealogy for service, safety and process improvement purposes. According to the APICS, the premier professional association for supply chain and manufacturing operations management defines “traceability” as: “the attribute allowing the ongoing location of a shipment to be determined” and/or “the registering and tracking of parts, processes and materials used in production, by lot or serial number.
Often, this effort involves manual processes or even paper-based recording and form-filing. Interest in track and trace has become more widespread in virtually all products and markets (both discrete and process) to create an audit trail that can be used in the case of a product issue or mandated recall. Simply tracking the receipt of raw materials and shipment of finished goods may fulfill the bare minimum requirements in some cases, but the real value of traceability increases exponentially when every movement and value-adding activity is tied together in an end-to-end historical chain.
Leverage barcode or RFID scanning to capture location and other data at any number of points along the supply chain or within a production facility.
Required track and trace for regulatory compliance (e.g., food safety such as E.coli or salmonella poisoning; or consumer product safety such as automotive airbag failures) requires the ability to measure the extent or exposure regarding the recalled product or components. Consider a recalled farm product.
If the manufacturer can identify the specific farm, shipment or batch that went into a tainted product, they may limit their exposure to a small subset of the products that contained that ingredient and not all of their production, saving them significant time, effort, and money.
To underscore the importance of real-time food traceability, the FDA requires that a traceability report be produced within 4 hours of being notified of a food safety event .Tracking can become challenging in the production environment with raw materials being split from their original shipping containers and used in multiple products throughout the facility. Effective track and trace brings a level of transparency with tangible benefits.
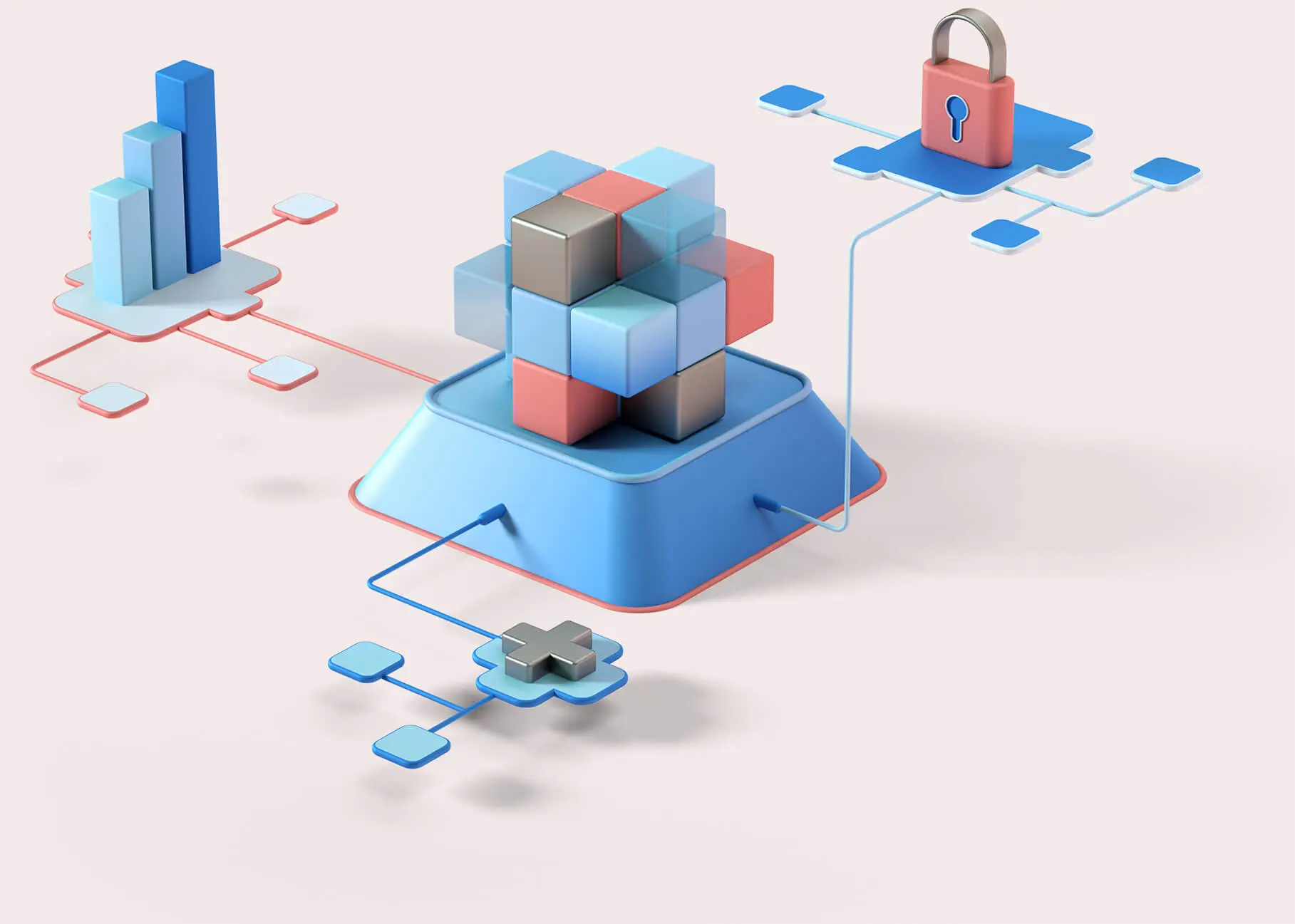
Real-time Visibility Across the Supply Chain with Oracle
Track and trace functionality is integral to the Oracle Manufacturing Cloud incorporating a rigorous tracking approach to record virtually every movement and operation in an unbroken chain of records to provide “high-resolution visibility.” It is often said that For every action in production, there is a transaction in Oracle. That translates into transparency that many groups within the organization can leverage.
Oracle can track individual parts, containers, or individual lots of ingredients including expiration dates and other critical information where appropriate. Barcode printing and scanning capabilities are built-in and tightly integrated so that all relevant information is consistent and controlled from the production database onto labels, including a library of customer-specified shipping labels that print automatically at ship time. Oracle records every transaction and makes it accessible and reportable at anytime from anywhere that you can access Oracle.
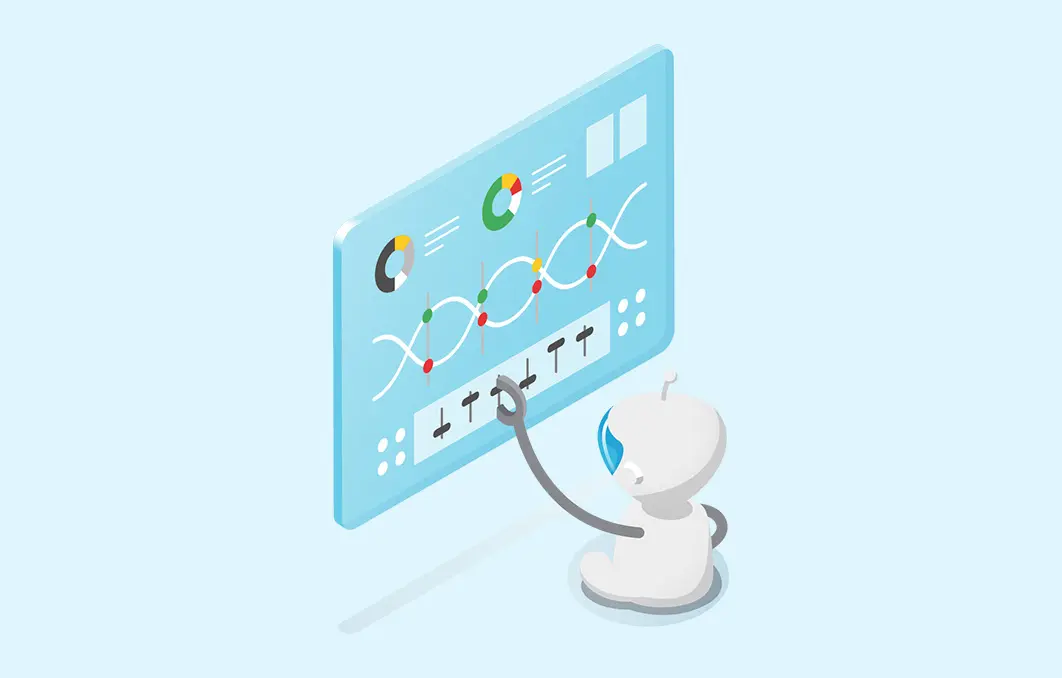
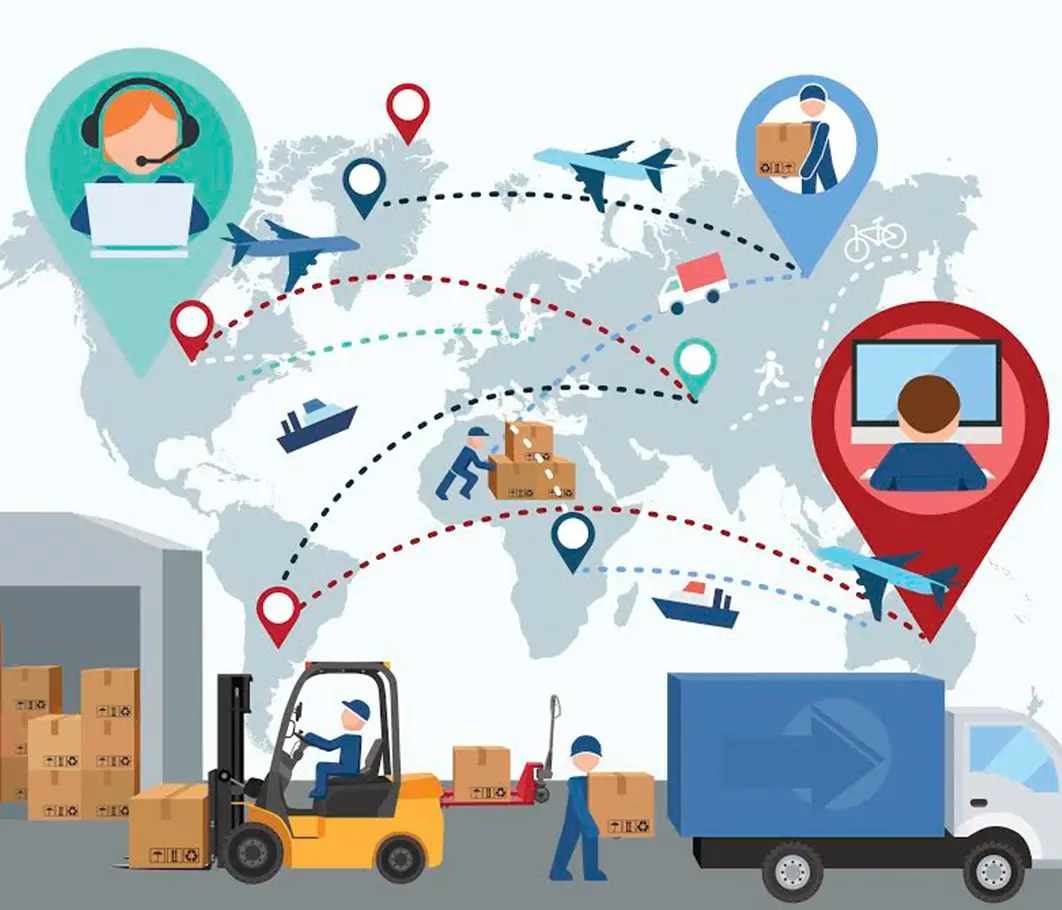
This level of traceability and genealogy creates a digital family tree that illustrates the parent-child relationship of each component and operation in production. Oracle automatically creates this genealogy including component details (batch/lot, etc.) production operations (date, machine, operator), and other information as desired. This traceability tree guides search and documentation both backwards and forwards (or upstream and downstream) from any item in question to its ultimate source or disposition.
Companies that only track incoming and outgoing goods are left with a gaping hole the production “black box” that limits the utility of track and trace. Oracle tracking gives manufacturers real-time visibility to inventory, including work-in-process, which enables them to reduce excess inventory that companies often maintain to reduce the impact of unexpected shortages or other surprises. Oracle brings significant benefits to the operations of a manufacturing organization, giving every department real-time visibility as to what is happening where. That visibility helps companies make sound operational and business decisions with confidence.
How lean are you? Learn the importance of effective inventory management and control.
ERP Software Solutions
-
Manufacturing ERP Software is not all the same. Historical ERP software solutions involve painful implementation projects followed by challenging periodical updates – often forcing companies to go years without updating their ERP system. Meanwhile these same companies lose value day after day as new features and functions elude them, only implemented with the next painful ‘big bang’ upgrade.
- Modern Manufacturing ERP Software from Oracle takes a different approach. No more waiting. No more upgrades. New features are added as you go, shared instantly with all Oracle cloud customers. These customers not only realize renewed value instantly, but share best practices real time with other peer customers, all of which have access to exactly the same features, functions and capabilities enabled by a true single ERP software code SaaS cloud offering.
- ERP software solutions should truly be just that, solutions. Manufacturers are often tempted by ERP software vendors touting strong financial accounting and even retail ERP software solutions and systems. None of these however do the one thing they need particularly well – manufacturing.
- With ERTechnologies Oracle is different, offering the only ERP software solution built from the ground up in the cloud and focused exclusively on manufacturing. At ERTechnologies we know manufacturing isn’t just part of our business, manufacturing is the business, The Oracle ERP manufacturing cloud software solution is purpose built to fit your manufacturing purpose needs, evolvingwith you while adding value daily.
- Manufacturing ERP Software is not all the same. Oracle can help you be different. Find out How.
ERP Systems
- Manufacturers have moved beyond the need for non-integrated point solutions to solve their challenges they require a true ERP system. Beyond individual bolt-on-products, an ERP system enables connectivity between companies and their suppliers all the time.
- An ERP system must fit the business needs of a given company, while offering a broad array of capabilities designed for that business. With an eye toward the future, the right ERP system enables connectivity between companies, their customersand their suppliers.
Why should you choose Oracle NetSuite Cloud for Inventory Traceability?
NetSuite is a single solution that can integrate and provide 360-degree view of every operation within a Distribution business.
Learn how ER Technologies helped our client to transcend ahead in the modern era with their NetSuite Solution.